Mastering efficient warehouse inventory management is a vital aspect of running a successful warehouse, especially as your warehouse increases in size and volume.By smoothly and accurately tracking and managing inventory as it enters, occupies, and exits the warehouse, managers get the information they need to design the best warehouse storage layout, maintain adequate stock levels, optimize safety stock and reorder times, and minimize wasted space.In this guide to efficient warehouse inventory management, we explore the most important best practices that warehouse managers should follow to effectively track, manage, and optimize the flow of inventory through any warehouse or fulfillment center. You’ll find answers to:
- What is warehouse inventory management?
- Is warehouse management the same as warehouse inventory management?
- What are some best practices for efficient warehouse inventory management?
- How can efficient warehouse inventory management support data-driven decision making for warehouse managers?
- How can battery-powered mobile workstations support efficient warehouse inventory management?
What is Warehouse Inventory Management?
Warehouse inventory management is the process of tracking, counting, managing, and overseeing inventory throughout the entire warehousing process—from receiving, through to storage, picking, and up until the inventory is sold and shipped to the customer.An efficient and accurate approach to warehouse inventory management allows warehouse managers to know what inventory they have in stock, maintain adequate inventory and safety stock levels for each SKU, optimize the warehouse storage layout, identify high-velocity SKUs, and even to anticipate or predict future demand for specific SKUs in inventory.
Warehouse Management vs. Inventory Management - What’s the Difference?
The terms “warehouse management” and “warehouse inventory management” often appear together and are sometimes used interchangeably - but from our perspective, they aren’t quite the same thing.Warehouse management is a high-level term that encompasses the management and optimization of all operational processes in the warehouse, such as receiving, putaway, storage, picking, packing, and shipping. Warehouse management isn’t just about inventory, it’s also about managing the people, processes, and technology needed to drive efficiency, accuracy, and overall excellence in warehouse operations.
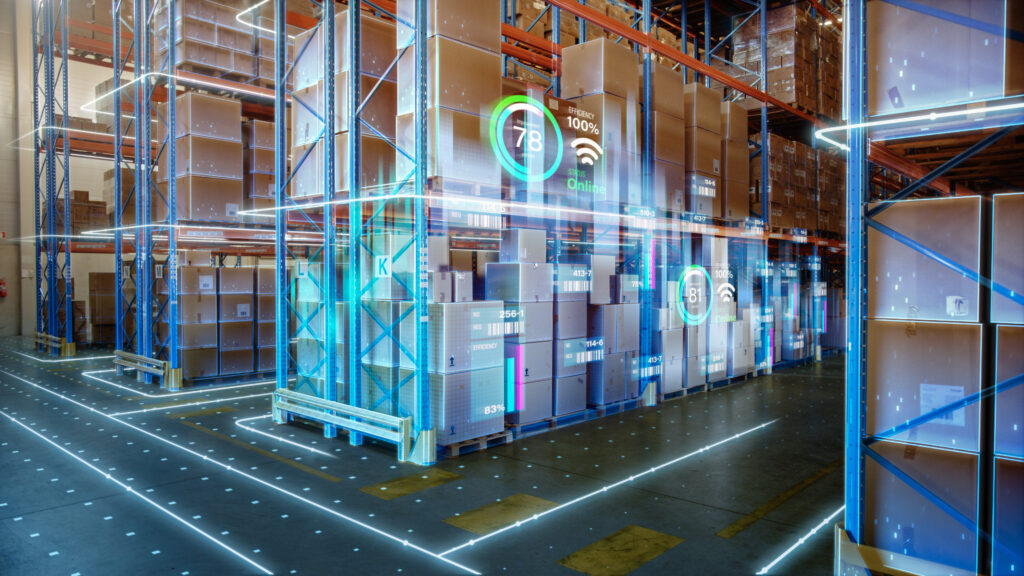
Warehouse inventory management is a more specific term that focuses on efficiently and accurately tracking inventory levels to help answer questions like:
- How much inventory do we currently have on-hand?
- Which SKUs are in stock or out of stock?
- How much inventory should be kept on-hand for each SKU?
- How should our inventory be stored/organized?
- When does inventory need to be ordered?
- How much inventory do we need to order?
- …and more.
Aspects of warehouse management and inventory management often overlap. For example, standardizing your warehouse receiving process is an essential aspect of both warehouse management (because it helps save time, reduce costs, and maintain good supplier relations) and inventory management (because it involves systematically counting inventory and recording counts in your inventory management system).
Two Warehouse Inventory Management Approaches You Should Know
Most warehousing operations follow one of the two most common approaches to inventory management: periodic inventory management, and perpetual inventory management.Below, we describe both approaches to managing warehouse inventory and what makes them different.
Periodic Inventory Management
Best for small businesses with low sales volume and a relatively small number of SKUs, Periodic inventory management relies heavily on manual processes, with workers counting inventory by hand to measure and record inventory levels. Some warehouses using periodic inventory management count all of their inventory at the same time each week, month, or quarter. Others implement a cycle counting system where SKUs are counted daily on a rolling schedule, usually over a period of 1-3 months.
Perpetual Inventory Management
Perpetual inventory management is a more modern approach to managing warehouse inventory that uses computer technologies to automatically count, track, and monitor inventory as it moves through the warehouse. With this system, products are assigned barcodes or RFID chips that make it easy for warehouses to track their movements in the warehouse using inventory management software solutions. When inventory is sold, transactional data from point-of-sale systems is fed back into the inventory management software to automatically update inventory counts for the affected SKUs. As a result, warehouse managers have real-time visibility into warehouse inventory levels.
9 Best Practices for Efficient Warehouse Inventory Management
1. Standardize Your Warehouse Receiving Process
The inventory management process begins when new inventory arrives in your warehouse receiving area, so it’s important to standardize that receiving process and ensure that critical steps are never missed. Your warehouse receiving process should ensure that new inventory:
- Conforms to any packaging requirements negotiated with your supplier
- Is inspected for damage before the shipment is accepted
- Is accurately counted and added to your inventory management system
Standardizing your warehouse receiving process helps ensure that inventory is consistently and accurately counted and represented in your inventory management system as it enters the warehouse.
2. Track All Products in Inventory
To facilitate an efficient approach to warehouse inventory visibility, warehouse managers need a formalized system for tracking all products in the warehouse.The most common methods for warehouse inventory tracking include:
- Excel Spreadsheets - Warehouses with low sales volume or a small number of SKUs may track inventory using spreadsheets. Stock is counted manually and inventory counts are updated in the spreadsheet by warehouse staff.
- Barcode/RFID Tracking - Warehouses with a greater sales volume and more SKUs can benefit from barcode or RFID-based inventory tracking that integrates with inventory management and financial software tools. Warehouse employees can use battery-powered mobile workstations equipped with barcode scanners or RFID readers to count inventory and update stock levels in the warehouse inventory management software system.
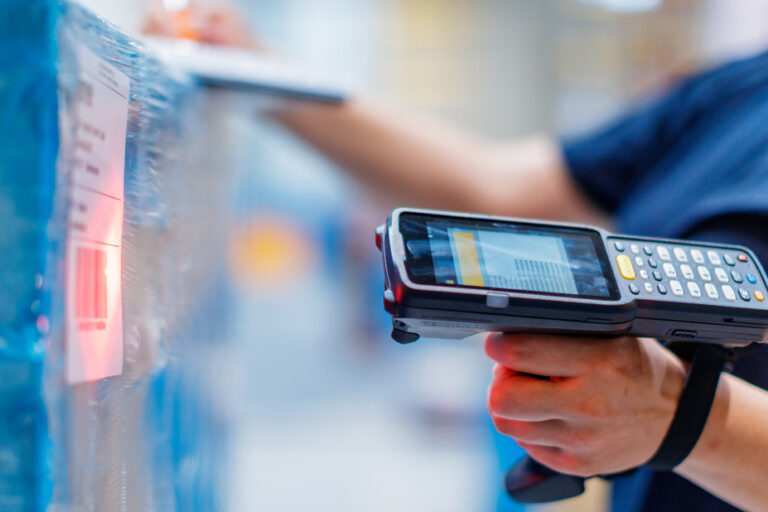
Barcode or RFID inventory tracking is the most efficient choice for inventory tracking, as it provides near real-time visibility of inventory levels in the warehouse while requiring less manual labor from warehouse employees.
3. Implement the ABC Method for Inventory Storage
In the ABC Method, SKUs in the warehouse are categorized based on their overall importance to the business:
- Category A is for fast-moving SKUs with high sales volume that contribute lots of revenue.
- Category B is for moderately important items that generate regular sales in low-medium volumes.
- Category C is for slow-moving SKUs that generally sell at low volumes and contribute little to overall warehouse revenue.
By dividing SKUs into these 3 categories, warehouse managers can optimize the warehouse storage layout to accelerate the order picking process and effectively prioritize tasks like counting and reordering to ensure that top revenue-generating items are kept in stock and available for sale.
4. Implement Warehouse Inventory Management Software
Warehouse inventory management software is the most efficient, accurate, and least labor-intensive way for large warehouses to track and manage inventory.With modern inventory management software, warehouse managers can achieve real-time visibility of inventory levels in the warehouse. Warehouse employees can scan products in/out of the warehouse, conduct inventory spot checks, or execute cycle counts using barcode scanners or RFID equipment. Additional features can include batch, lot, and serial number tracking, automated reordering, demand forecasting, and integrations with shipping carriers, eCommerce/POS systems, and financial tools.Warehouses using legacy inventory management methods like Excel Spreadsheets should consider implementing inventory management software to improve overall visibility of inventory and support data-driven decision-making with respect to inventory management.
5. Track Sales and Monitor Sales Trends
As inventory is sold, it leaves the warehouse for delivery to the customer and must be removed from the inventory management system. To do this accurately, warehouse managers need a system for accurately tracking sales, ensuring that sold items are removed from the organization's inventory management system, and monitoring sales trends over time.Some warehouse managers are still tracking sales with traditional manual processes and using legacy tools like Microsoft Excel to track sales and update inventory counts on a daily or weekly basis.But with the right technology, warehouse managers can integrate data from point-of-sale and financial software systems with inventory management software tools to automatically update stock levels when inventory is sold. This approach is more efficient because it minimizes the need for error-prone manual data entry.Monitoring sales trends over time also gives warehouse managers the ability to predict or forecast demand for individual SKUs and adjust their order quantities to avoid out-of-stock situations.
6. Use Cycle Counting or Audits to Verify Inventory Levels
Even warehouses that take a software-driven approach to inventory management need processes for manually counting stock to verify inventory levels and check for discrepancies between actual and recorded inventory counts.Some warehouse managers choose to count all of their stock at the same time - typically either weekly, monthly, or quarterly depending on the size of the warehouse. Others do an annual inventory audit where all SKUs in the warehouse are counted. This process can take several days and may disrupt the regular flow of business.A more efficient approach to verifying inventory levels is known as cycle counting. Instead of counting inventory for all SKUs at the same time, warehouse employees count a handful of SKUs on every shift using a schedule that ensures every single SKU is counted at least once during a specified time period.Cycle counting transforms the task of auditing inventory levels from a complex monthly project into a simple daily task that minimizes disruption to the business while providing warehouse managers consistent feedback on inventory levels.
7. Measure Lead Times and Calculate Reorder Points
With systems in place to track sales and inventory levels, warehouse managers can implement accurate and efficient processes for keeping the warehouse stocked and ensuring high-velocity SKUs are always available to order. This includes measuring lead times and calculating reorder points for each SKU.The lead time for a given supplier is the average time it takes for that supplier to fulfill an order. If a supplier has a lead time of 3 weeks to deliver inventory of a given SKU, you’ll need to place your order at least 3 weeks before you actually need the new inventory in your warehouse.Warehouse managers calculate reorder points to determine when they should replenish stock in a given SKU. The reorder point for a SKU depends on its sales velocity and lead time. For example, if a warehouse sells 50 widgets per week and the lead time for ordering more widgets is 3 weeks, the warehouse manager should order widgets when they have around a 3-week supply left in stock - in this case, around 150 widgets.Tracking average lead times for suppliers helps warehouse managers determine when orders should be placed to keep their most important items in stock.
8. Optimize Safety Stock Levels
Another thing warehouse managers can do with inventory tracking is calculate optimal safety stock levels for every SKU in the warehouse.Safety stock is an extra or additional quantity of a SKU that's stored in a warehouse to avoid out-of-stock situations in cases where an expected shipment is delayed and the stock would otherwise run out. Maintaining adequate safety stock is especially important for Category A items that contribute a lot of revenue to the warehouse.Safety stock levels are also related to lead time and SKU velocity. A rule of thumb for calculating safety stock levels is to keep on hand 50% of the amount of stock used during a SKU's lead time. If a warehouse sells 50 widgets/week and the lead time for ordering more widgets is 3 weeks, the warehouse should keep 50% of a 3-week supply in safety stock - in this case, that would be 50% of 150 widgets, or about 75 widgets.
9. Enhance Inventory Management Efficiency with Mobile Workstations
Battery-powered mobile workstations for the warehouse bring inventory management software and barcode/RFID technology directly to the point of task, allowing warehouse employees to count new inventory, execute spot checks or cycle counts, and pick orders faster and with fewer errors.
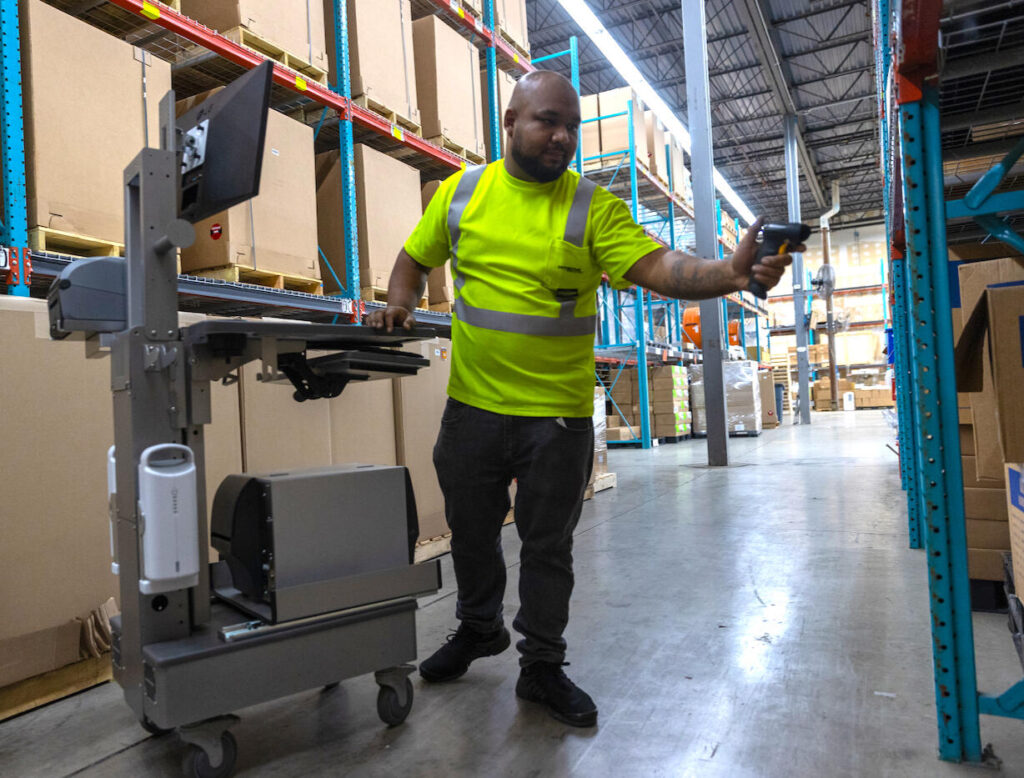
Why is Efficient Warehouse Inventory Management Important?
Minimize Waste
Poor inventory management in the warehouse creates waste, especially in the form of poor storage utilization, carrying too much safety stock in the wrong items, and having too many out-of-stock events that lead to lost sales.
Monitoring Shrinkage
Inventory shrinkage is lost inventory due to theft, fraud, damage, or administrative error. Warehouse managers can leverage inventory management processes like cycle counting to identify discrepancies between actual and recorded inventory levels, then write off the lost inventory or conduct an investigation to determine the cause of the shrinkage.
Faster Order Fulfillment
A warehouse with strong inventory management can fulfill orders faster. The locations of items are well-known, high-velocity SKUs are readily accessible, and the warehouse is adequately stocked.
Enhanced Customer Satisfaction
Efficient inventory management can have a direct impact on enhancing customer satisfaction. Strong inventory management processes help ensure that SKUs are adequately stocked and available to order, and that orders can be quickly fulfilled and delivered to the customer.
Improved Cash Flow
Poor inventory management processes can lead to mismanagement that negatively impacts cash flow for your warehouse. This includes ordering too much inventory of slow-moving SKUs, retaining too much safety stock, or failing to adequately replenish inventory of high-velocity SKUs, which results in stock-outs and lost revenue.Maintaining strong inventory management practices allows warehouse managers to make data-driven ordering and inventory decisions that optimize cash flow for the business.
Reduced Warehousing Costs and Increased Profitability
Efficient warehouse inventory management helps reduce warehousing costs and drive increased profitability by optimizing space utilization, accelerating order picking and fulfillment processes, and reducing shrinkage and waste.
Maximize Inventory Management Efficiency with DTG Mobile Workstations
Whether your warehouse manages inventory using manual counts and spreadsheets, or with barcode/RFID counting and software technology, DTG’s battery-powered mobile workstations can help your employees perform critical inventory management tasks faster and more accurately with fewer wasted steps.
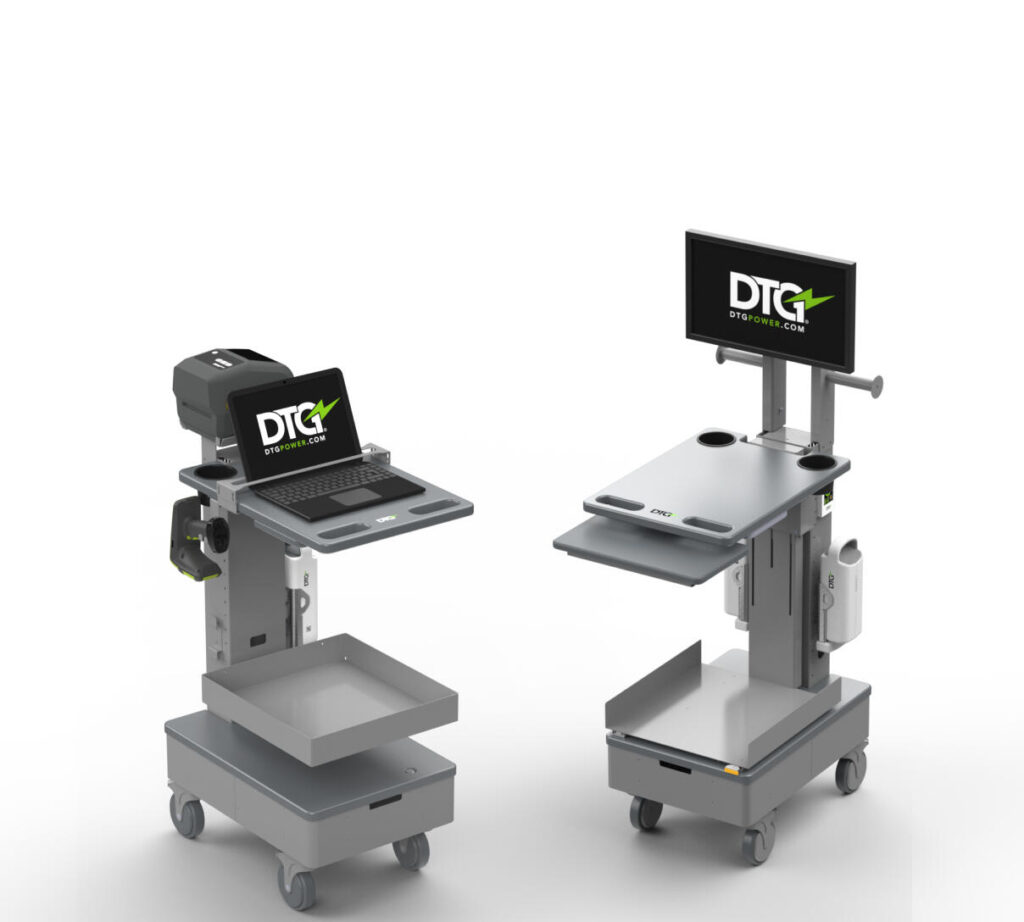
Our Problem Solver warehouse cart is durable, ergonomic, and easily configured with computers, peripherals, and barcode/RFID technology for optimized inventory management. Plus, our warehouse carts are powered by ultra-safe and reliable LFP battery systems with hot-swapping capabilities that guarantee 24/7 uptime for your mobile workstations.
Ready to learn more?
Request a Demo with our team and discover how you can optimize warehouse inventory management and other key processes with DTG mobile warehouse carts.