LSS SERIES #1: The Meaning, Phases, and Benefits of Lean Six Sigma
LSS combines Six Sigma methods and tools with the lean manufacturing/lean enterprise Philosophy. It strives to eliminate the waste of physical resources, time, effort, and talent while assuring quality in production and organizational processes.
What Is the Meaning of Lean Six Sigma?
Lean Six Sigma is a process improvement strategy that seeks to eliminate inefficiencies in a company's process flow by identifying the causes of waste or redundancy and developing solutions to address them.
DMAIC: Approach to Continuous Improvement. What is DMAIC?
The DMAIC phases of Lean Six Sigma are Define, Measure, Analyze, Improve, and Control. The DMAIC process is data-driven and drives through every intricate detail. It offers comprehensive ways to improve a business process or function. This model is applicable in every industry or field. However, it is best known for its symbolic contribution and application in Six Sigma and Lean Six Sigma.[embed]https://youtu.be/dgvLyWJYR0s?si=V6nI18_sF_uTd7ll[/embed]
The Phases of DMAIC
Define
Define the problem from a company perspective, stakeholder perspective, and customer perspective. Figure out the quality expectations that customers have and the extent of the problem.
Measure
Examine the current process and how it contributes to the problem. Determine whether the process can meet the previously defined quality expectations of customers. Match each process step to your quality criteria. Support your measurements with actual performance data.
Analyze
Examine all information gathered thus far to finalize the exact nature of the problem, its scope, and its cause.
Improve
Solve the problem and verify the improvement. Collaborate to structure a solution that eliminates both the problem and its cause. Use your data to ensure that the solution fits the issue at hand. Test the solution and derive performance data to support it.
Control
Monitor improvement and continue to improve where possible. Finalize acceptable performance criteria. Establish a plan that can deal with variations that occur, sustain improvements, and prevent a recurrence of the original problem.
DMAIC and Six Sigma Relations
Six Sigma DMAIC uses the same concepts and applies them to create and solve Six Sigma projects. Six Sigma is oriented towards making a process or function more effective, and what better way to achieve it than by using DMAIC?Although Six Sigma uses much more than just DMAIC and uses a lot of tools, data, and statistics, Six Sigma projects and its applications form their core around DMAIC.
How Do Lean and Six Sigma Work Together?
Lean helps you to streamline processes, while Six Sigma works to improve quality by reducing errors or variations. Both methods focus on developing optimally performing processes.
What are the Benefits of Lean Six Sigma?
You will gain so many benefits from correctly implementing Lean Six Sigma.
- Less Waste, Defects & Variation
- Lower Costs
- More Savings
- Increased Profits
- Improved Efficiency
- Higher Team Engagement
- Better Processes
- Consistent Quality
- Shorter Cycle Times
- Problem Solving Skills
- Faster Lead Times
- Increased Capacity
10 Questions to Point You in the Right Direction
If you're unsure whether Lean Six Sigma is the right solution for your company, take a quick read through the following questions. If your answer is "yes" to any of the questions below, Lean Six Sigma could be the right choice for you.
- Do you want to identify and eliminate non-value-add tasks in your workplace?
- Do you want to find effective solutions to flaws in your processes, projects, or projects?
- Are you looking for a fresh way to tackle existing problems in your working environment?
- Would you like to standardize processes in your company, team, or department?
- Do you have a need / want to future-proof a product or service?
- Are you seeking ways to cut down waste in your business?
- Are you aiming for more consistent, predictable results?
- Is increasing productivity a goal for you?
- Do you need to reduce costs?
- Do you feel you would benefit from using a proven method for achieving results?
A Vital Role in Lean Six Sigma: Process Owner
Examine more closely the companies which are sustaining the gains from their Lean Six Sigma efforts and you will find the process owner. A process owner in Six Sigma is a senior business executive, who is in charge of the business process that a Six Sigma project is trying to improve.Businesses are realizing that Lean is a commitment, a journey that takes your organization to new levels of efficiency and smart thinking at every stage.
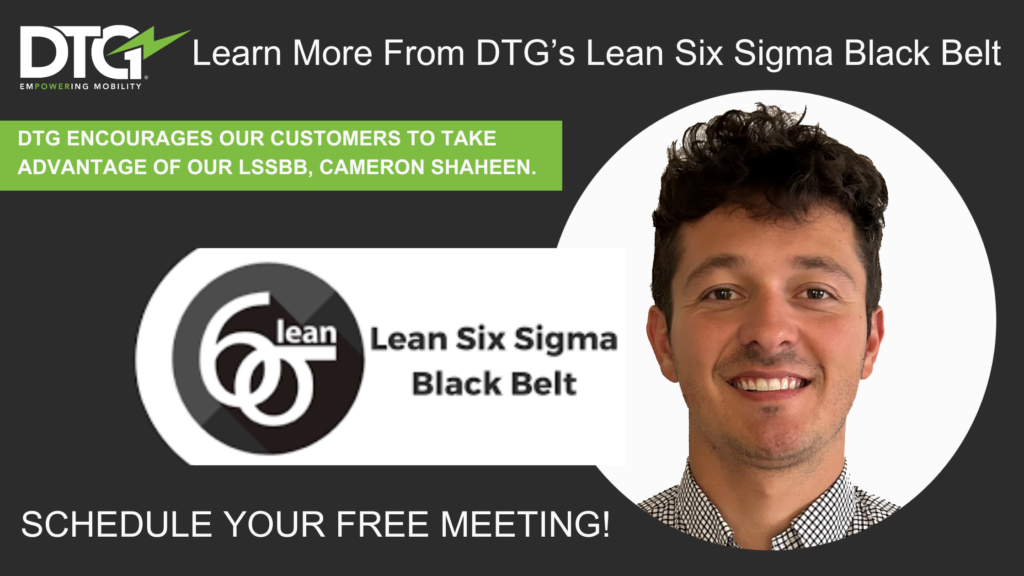