LSS Series #4: DMAIC and Lean Six Sigma Phase 5: CONTROL
Welcome back to DTG’s Lean Six Sigma Series! In this final step of the DMAIC process you should have uncovered all waste and inefficiencies and have developed a plan to solve them. By learning the LSS methodology and understanding its value, you have brought a valuable resource to your organization’s operation.

PHASE 5: CONTROL
Maintain the solution(s)
How do you sustain the newly achieved improvement? This phase is a mini version of process management. The team has been building a form of infrastructure throughout the life of the project, and during the Control Phase they begin to document exactly how they want to pass that structure on to the employees who work within the process.
Continuously improve the process using Lean principles
The four principles of Value, Flow, Pull and Perfection should remain a constant focus for every organization. As Continuous Improvement teams hand over the results of each project, they must make efforts to relay this focus to the employees using the newly improved process. The process can always be improved.
- Value: Determine what steps are required (are of “Value”) to the customer
- Flow: Remove Waste in the system to optimize the process to achieve a smoother pace
- Pull: Ensure the process responds to customer demand (“Pull” = want)
- Perfection: Continuously pursue “Perfection” within the process.
Ensure the process is being managed and monitored properly
In order to maintain this focus, the team must narrow down the vital few measurements they want to maintain for ongoing monitoring of the process performance. This monitoring is accompanied by a response plan indicating the levels at which the process should operate and what to do in the case that the process should exceed those levels. Identify what the key performance indicators are for a healthy process and set a standard for if the process is in control or out of control. This may lead to continued process refinement.
Expand the improved process throughout organization
At this point, the team must update their documentation: process maps, document checklists, cheat sheets, etc. The better their final documentation, the easier it will be for process participants to adopt the new way of doing things. This includes training and educating the process owners and participants to understand the why and how behind the new process.
Apply new knowledge to other processes in your organization
One of the ways to increase the power and “bang for the buck” of Lean Six Sigma efforts is to apply the gains from one project into other areas within the organization. This transfer of improvement ideas can come from large and small efforts but quickly multiplies the impact for each business.
Share and celebrate your success
The sharing of project success leads to greater momentum of change within the organization. Even if the project cannot be transferred to other areas, there may be parts of it that could be adapted and shared. The marketing and publicizing of each success increases the speed with which future gains can be realized. Lean Six Sigma success drives more success.
Did you know we offer our customers a suite of complementary Lean Six Sigma services with DTG LSS Black Belt, Cam Shaheen?
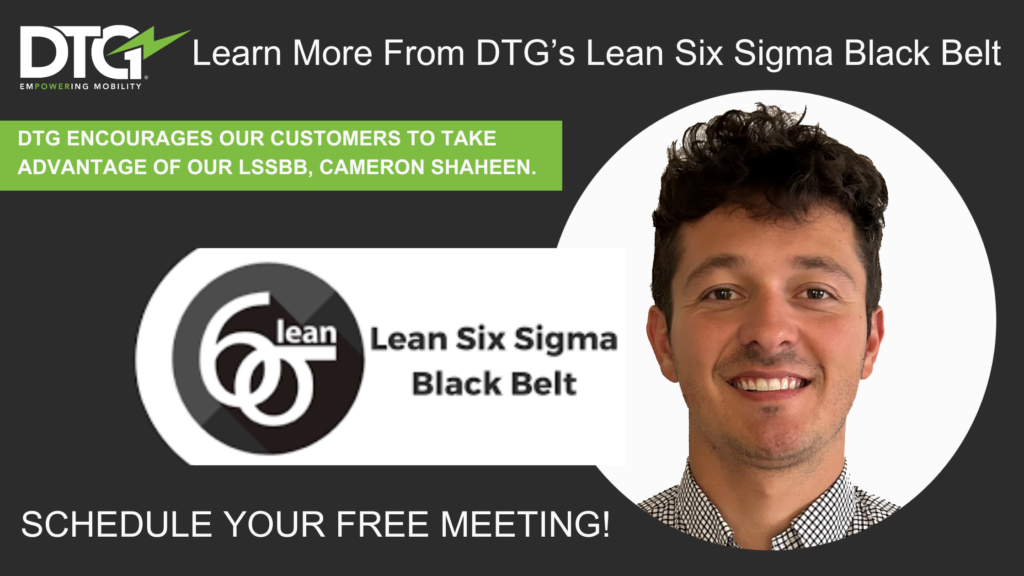