[vc_row][vc_column][vc_column_text]
LSS Series #4: DMAIC and Lean Six Sigma Phase 4: IMPROVE
Welcome back to DTG’s Lean Six Sigma Series! This is the creative step in the DMAIC process where you begin to brainstorm on possible solutions resulting from all the data you have collected up to this point. To review, in the Analyze Phase, we identified the cause of the problem by performing a Process Analysis. Now, the Improve Phase begins.
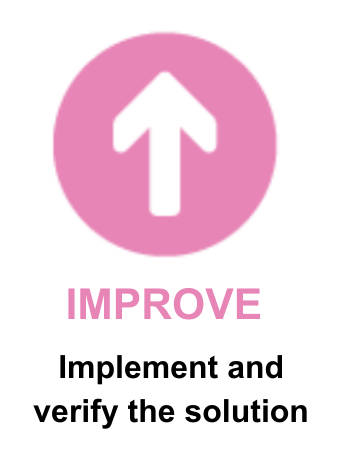
PHASE 4: IMPROVE
Implement and Verify the Solution(s)
How will you fix the problem? Once the project teams are satisfied with their data and determined that additional analysis will not add to their understanding of the problem, it’s time to move on to solution development. The team is most likely collecting improvement ideas throughout the project, but a structured improvement effort can lead to innovative and elegant solutions.
Brainstorm solutions that might fix the problem
The team's efforts at this stage are to produce as many ideas as possible based on the idea that from Quantity, comes Quality. Creative idea generation consists of a host of techniques intended to lead the team to out-of-the-box solutions.Review how others in your industry are handling these problems. There is always someone else that is farther along in the improvement process than them that may have already identified and implemented solutions.
Select the practical solutions
In many cases, a project team can employ a list of improvements to their processes, but when they are forced to choose between conflicting options, there are tools like the “Weighted Criteria Matrix”, which helps your team make the best decision.
Develop maps of processes based on different solutions
With solutions in mind to reduce rework loops, waste and wait times, the team can draw an improved map of the process, also known as “To-Be Maps.” These new maps are helpful in guiding the team’s efforts toward the new process, and can be used as a reference for new employees as they are trained on the new process.
Implement the solution(s)
Accomplishing successful implementation requires careful planning. The team must consider logistics, training, documentation and communication plans. They also verify how the solution(s) impact people across the organization to ensure it does not create problems for other parts of the organization. The more time the team spends on planning, the faster they reach total adaptation to the improvements by their process participants.
Measure improvement
Once the team is able to show that the solution has resulted in measurable improvement, then the team can move on to the Control Phase.
Did you know we offer our customers a suite of complementary Lean Six Sigma services with DTG LSS Black Belt, Cam Shaheen?
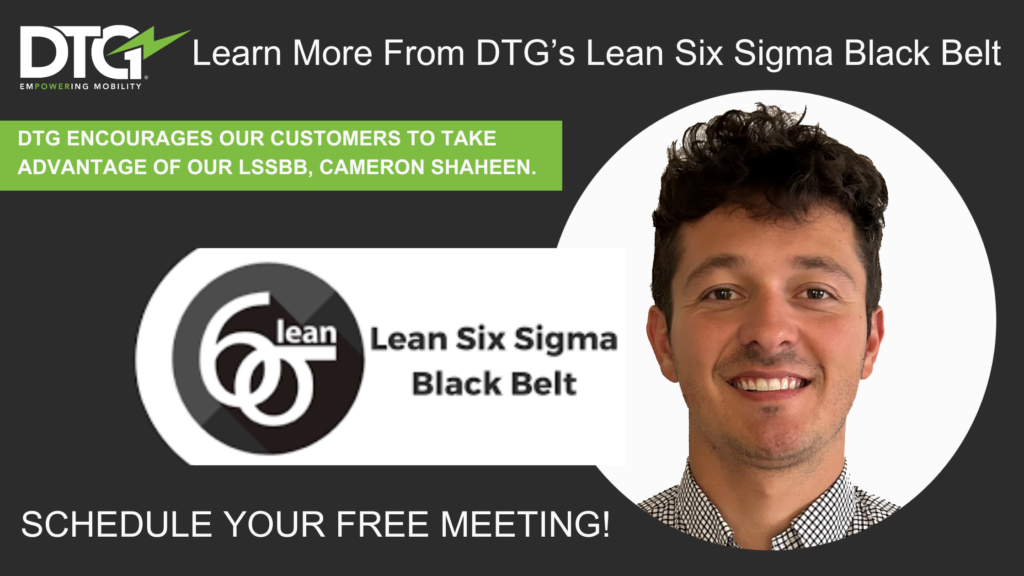
Click here to schedule your FREE meeting! [/vc_column_text][/vc_column][/vc_row]