LSS Series #4: DMAIC and Lean Six Sigma Phase 3: ANALYZE
Welcome back to DTG’s Lean Six Sigma Series! Now we are halfway through the DMAIC process and hopefully you are beginning to grasp the importance of this methodology and how it will help you uncover inefficiencies and different types of waste in your operations leading to improved productivity and efficiency.In the Measure Phase, we created a data-collection plan, a critical piece of the process since reliable data is key to good decision making. Now, the Analyze Phase begins.
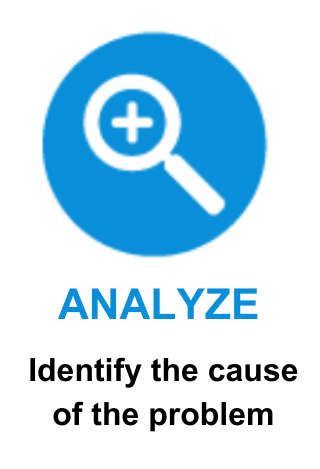
PHASE 3: ANALYZE
Identify the Cause of the Problem
What does your data tell you? This phase is often intertwined with the Measure Phase. As data is collected, the team may consist of different people who will collect different sets of data or additional data. As the team reviews the data collected during the Measure Phase, they may decide to adjust the data collection plan to include additional information. This continues as the team analyzes both the data and the process in an effort to narrow down and verify the root causes of waste and defects.
Closely examine the process
After creating, verifying and examining detailed process maps created in the Measure Phase, the team will be able to list concerns or pain points within the process. This allows the team to take advantage of the collective wisdom of process participants. Then, the team can determine the value of each step by performing analyzing the process by performing “Process Analysis” which consists of:
- “Time Analysis“: focuses on the actual time work is being done in the process versus the time spent waiting.
- “Value Added Analysis“: adds another dimension of discovery by looking at the process through the eyes of the customer to uncover the cost of doing business.
- “Value Stream Mapping”: combines process data with a map of the value-adding steps to help determine where Waste can be removed.
Visually inspect the data
After data collection, the team will be able to display the data using charts and graphs for visual indications for problems in the process. The transformation of numbers into visuals allows the team to easily communicate their findings to leadership and other process participants.
Brainstorm potential cause(s) of the problem
Teams are able to develop theories around possible causes of the problem by brainstorming together. By using a tool called a “Cause & Effect Diagram“, the teams are able to perform structured brainstorming that can help them narrow down to the vital few causes of lost time, defects and waste in the process.
Verify the cause(s) of the problem
Before moving on to the next phase (Improve), the team must confirm the proposed root cause is creating the problem by verifying their data through process analysis, data analysis, process observation and comparative analysis.
Update your Project Charter
After the team has further investigated the data, they will have additional detail around process performance and the potential for improvement. The team can update their Charter with the additional information so they have a more accurate reflection of the project status.
Did you know we offer our customers a suite of complementary Lean Six Sigma services with DTG LSS Black Belt, Cam Shaheen?
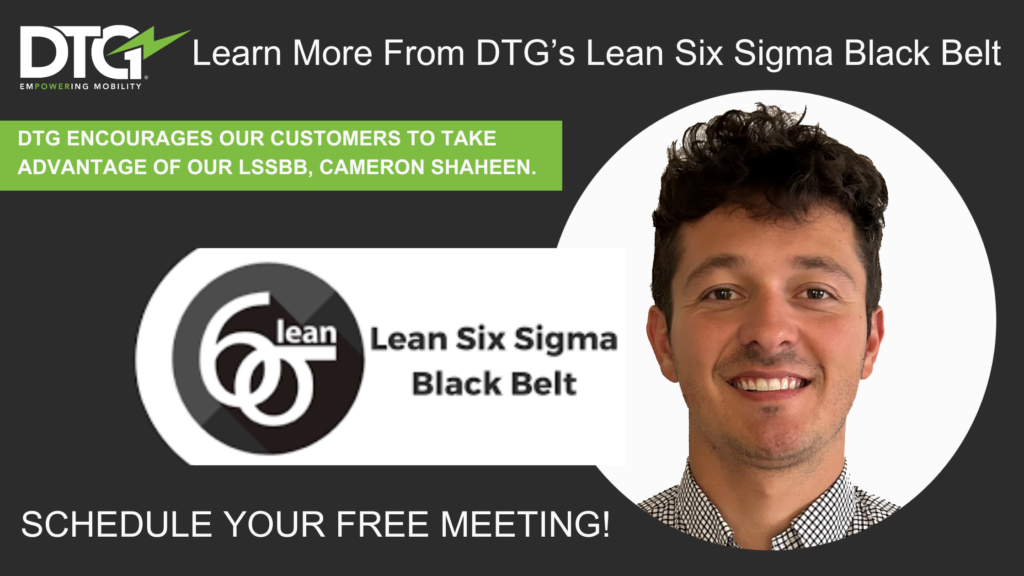