LSS Series #3: DMAIC and Lean Six Sigma Phase 2: MEASURE
Welcome back to DTG’s Lean Six Sigma Series! Understanding this methodology will help you uncover inefficiencies and different types of waste in your operations and will improve your productivity and efficiency factor.As we learned in the Define Phase, a “Project Charter'' was created, a high-level view of the process. Here we begin to understand and quantify the problem we are trying to solve. Now, the Measure Phase begins.
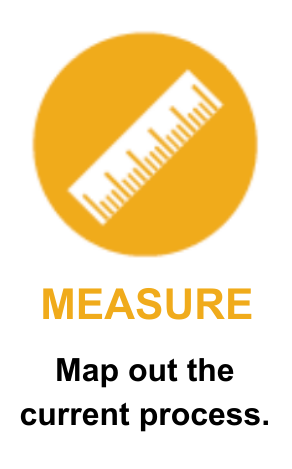
Map out the current process
How is the process currently performed? Measurement is critical throughout the life of the project and as the team focuses on data collection, initially they have two focuses:
- Determining the start point or baseline of the process
- Looking for clues to understand the root cause of the process.
Since data collection takes time and effort it’s good to consider both at the start of the project. Utilize the process map and identify where the problem is occurring in the process steps.
Determine how the process currently performs
First, your team must establish the current state, or the “baseline” of the process before making any changes. The baseline becomes the standard against which any improvement is measured. This is a key step as the data collected will be used throughout the life of your project.
Create a Plan to Collect the Data
Once the team clarifies the baseline measure, they must consider where to get the data:
- How much to collect
- Who will get it and how
- How to collect the data
A well-thought-out Data Collection Plan is critical since accurate and reliable data are key to good decision making.
Ensure the Data is Reliable
Defining and refining process measures leads to collecting critical process information. This enables the team to make good project decisions. Reliable data ensures corrective actions are based on facts rather than assumptions and opinions.
Gather the Baseline Data
Data collection generally involves gathering system information, creating reports and manually collecting process information when it’s not readily available. Leverage SMEs and process owners to help ensure you are collecting accurate data. Next, go to where the process takes place (go to GEMBA) to see if there is waste that has not been accounted for. Watching the process take place can give insights you may not have thought about in project charter.
Update Your Project Charter
A project charter in Lean Six Sigma is a two-page document that outlines a process improvement project. The charter contains data-driven information explaining the need for the project.Initial data collection efforts provide the team with helpful details around process performance and potential targets. The team refines their Project Charter with new data that more accurately reflects the problem and the goal. This process of refinement continues into the Analyze Phase.
Did you know we offer our customers a suite of complementary Lean Six Sigma services with DTG LSS Black Belt, Cam Shaheen?
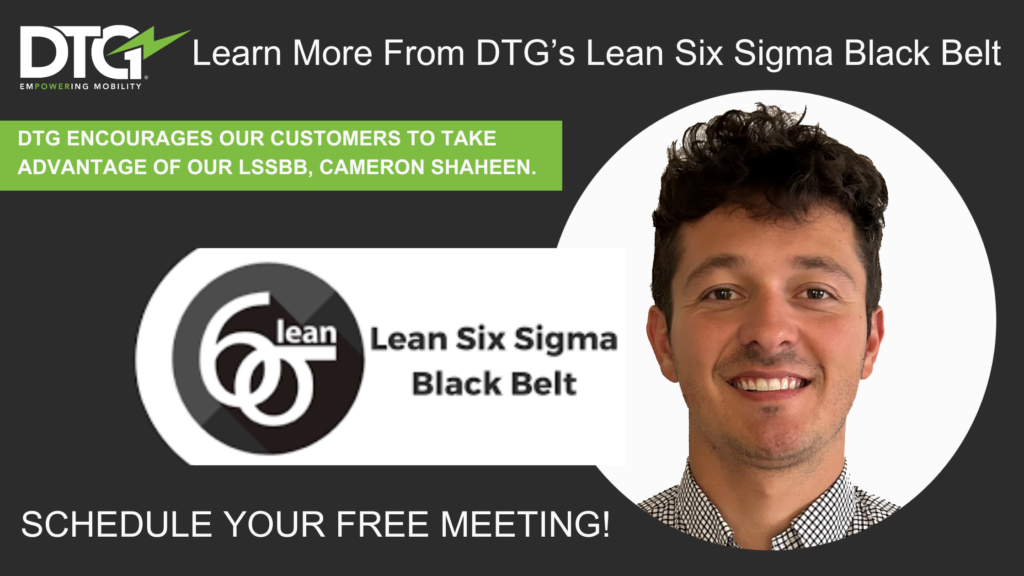