Warehouse quality control is more than just ticking boxes; it's an essential aspect of running a successful warehouse that continuously improves efficiency, drives customer satisfaction, and keeps your warehousing business running smoothly and profitably.In this ultimate guide to better quality control in the warehouse, we’ll dive deep into the implementation and explore the strategies, tools, and technology needed to transform your operations.Whether you're a seasoned logistics expert looking to fine-tune your processes or a newcomer seeking to build a foundation of excellence, this guide will equip you with the knowledge and insights to effectively implement quality control in your warehousing business.
What is Warehouse Quality Control?
Quality control in the warehouse setting is the systematic, ongoing process of ensuring that products and materials received, stored, picked, and shipped from a warehouse or distribution center consistently meet or exceed both predetermined internal quality standards and customer expectations.Modern quality control originated in Medieval crafting guilds and matured in American and Japanese automobile factories of the 1950s, with industrial innovators searching for ways to maintain manufacturing standards and minimize defects.Since then, quality control strategies and methods have been adopted by software developers, medical device manufacturers, warehousing distribution companies, and other industries as a means of ensuring that business-critical products, services, and process outcomes are delivered in accordance with predefined specifications, requirements, or quality standards.
Quality Control vs. Quality Assurance - What’s the Difference?
Quality control and quality assurance are often used interchangeably, but warehouse managers should understand the differences between these closely connected quality concepts.Quality assurance is a process-oriented set of activities with a focus on optimizing production processes and proactively preventing manufacturing defects or errors.Quality control is a product-oriented set of activities that focuses on testing or inspecting products, services, or other process outcomes to identify quality issues and verify conformity with established quality standards.[caption id="attachment_7027" align="aligncenter" width="1024"]
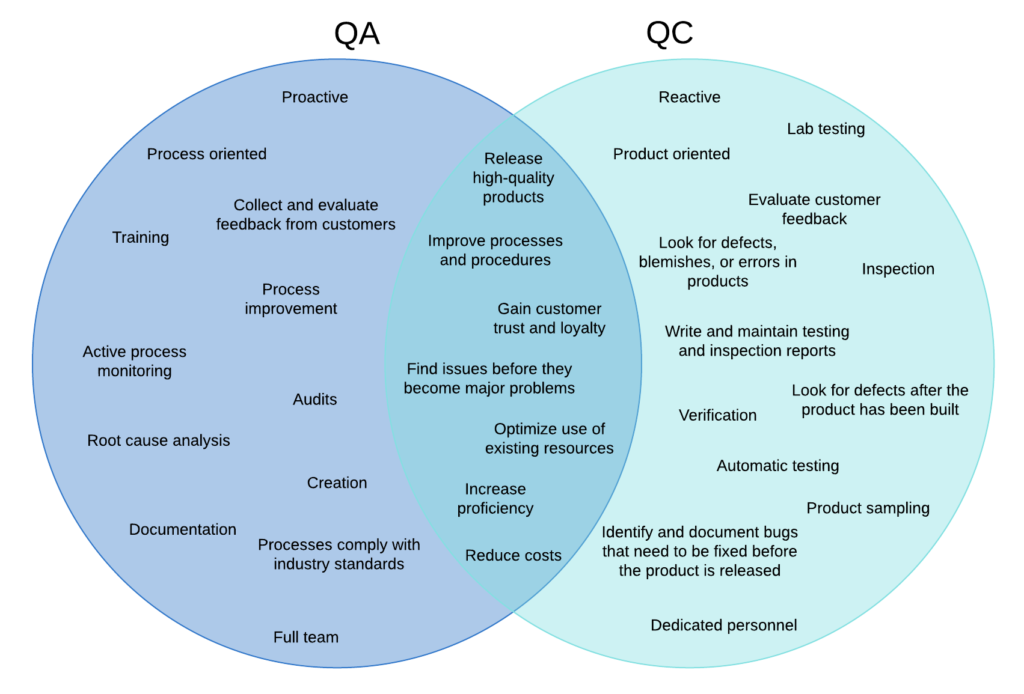
Image Source: Lucidchart[/caption]While QA tries to optimize processes and prevent defects, QC involves inspecting or testing the outcomes of those warehouse processes to ensure that quality standards are being met, identify opportunities for improvement, and to avoid sending defective shipments to customers.
Warehouse Quality Control vs. Manufacturing Quality Control—What’s the Difference?
Quality control is frequently discussed in the context of factories and manufacturing businesses who build products that must conform to specified requirements or quality standards. But warehouses aren’t manufacturers. Warehouses receive, store, and ship products, but they typically don’t build them - so how exactly does quality control apply?As it turns out, quality control and quality assurance can be applied to any process designed to achieve a measurable outcome. In manufacturing, QC is applied to the manufacturing process where the goal is to construct a product that meets predetermined requirements for form and function. In warehousing, we can apply QC to any internal warehouse process whose outcome can be measured, including processes like receiving, putaway, order picking, packing, and shipping.While a manufacturer might QC their product line outputs to ensure that all widgets meet product specifications, a warehouse manager might QC their outgoing orders to verify that orders are being picked, packaged, labeled, and shipped accurately to conform with internal standard operating procedures (SOPs) and ensure customer satisfaction.
What are the Goals of Warehouse Quality Control?
- Driving Customer Satisfaction
- The most important goal of all quality activities in the warehouse is to drive customer satisfaction. This means ensuring that customer orders are accurately picked, correctly packaged, and delivered to the customer in a timely fashion. Receiving inspections, in-process inspections, and outgoing order inspections can all play a role in driving customer satisfaction.
- Reducing Waste and Minimizing Costs
- A secondary goal of warehouse quality control is to reduce waste and minimize warehousing costs. QC inspections of outgoing orders can prevent defective orders from shipping to customers, lowering returns and reverse logistics management costs for the warehouse. QC inspections of incoming inventory give warehouse managers the opportunity to identify defective or mislabeled shipments from suppliers that can lead to shrinkage, dissatisfied customers, or high return rates.
- Maximizing Process Efficiency
- QC focuses on identifying defects, while QA is more focused on optimizing process efficiency. However, QC activities can feed directly into QA. When a quality control inspection reveals a defect or operational error, warehouse managers should conduct a root cause analysis to understand how the error happened, then implement corrective/preventive action to reduce the risk of it happening again. Over time, this feedback cycle should help the warehouse minimize preventable mistakes and improve the overall efficiency of its operational processes.
Making the Business Case for Warehouse Quality Control
Quality control is a great idea for almost any logistics or warehouse distribution center, but many neglect to implement clear quality standards or quality control processes due to the perceived high cost of quality programs.What’s often missing from that analysis is a quantified assessment of the value that warehouse quality control can provide. Just by inspecting outgoing orders and blocking defective or inaccurate orders from being shipped to customers, a QC initiative can increase business revenue, boost customer satisfaction, lower warehouse storage costs, drive down reverse logistics costs, and encourage repeat business. Plus, the results of these QC inspections can help direct process improvements that make warehousing operations more efficient and less expensive.To make a business case for quality control in your warehouse, we recommend tracking process outcomes using warehouse efficiency metrics or KPIs, identifying processes where quality issues frequently arise, and quantifying the cost of those issues to your warehousing business. The larger your warehousing operation, the greater a financial impact you can make with effective quality control.
Implementing a Successful Warehouse Quality Control System
Planning Quality Inspections in the Warehouse
The first step to implementing quality control in your warehouse is to identify key points in the warehouse inventory life cycle where quality inspections should take place. Three of the most common types of warehouse QC inspections are:
- Receiving Inspections - A process where newly received inventory is checked by quality personnel to ensure it was received in accordance with your defined warehouse receiving process/workflow. Receiving inspections can include documentation review as well as checking for labeling mistakes or damaged/missing inventory.
- In-process Inspections - In-process inspections can be implemented at any point in the warehousing life cycle. Quality personnel might inspect a storage bin to check for mislabeled or misshelved products and identify quality issues in the putaway process.
- Outgoing Order Inspections - Outgoing order inspections are common in warehouse quality control. Inspecting outgoing orders for quality helps ensure that customer orders are picked accurately, packed appropriately, and labeled correctly to ensure an excellent customer experience.
Warehouses can launch their quality initiatives by inspecting newly received inventory and outgoing orders, then monitor process metrics to decide whether/how in-process inspections should be implemented.
Establishing Quality Standards
Once you’ve decided when your quality control inspections will be conducted, the next step is to establish clear quality standards that will form the criteria for those inspections.If you’re inspecting new inventory that’s being received into the warehouse, your quality standards might include verifying that:
- The inventory is not damaged or defective
- The inventory packaging is not damaged or defective
- The inventory was counted and reported accurately
- The inventory was labeled or barcoded correctly
- The receiving documentation was completed correctly
- All relevant SOPs and workflows for the warehouse receiving process were correctly completed and documented
If you’re inspecting orders that are being shipped out of the warehouse, your quality standards might include verifying that:
- The order contains all items purchased by the customer
- The order does not contain any extra items
- The order was packed and packaged correctly to minimize shipping costs and prevent damage in transit
- The packaging materials used were appropriate for the order
- All relevant SOPs and workflows related to order picking and packaging were correctly completed
Ultimately, the quality standards for each inspection should be based on ensuring customer satisfaction, minimizing costs, and ensuring that processes are completed as efficiently as possible.
Implementing Quality Inspections
Once you’ve decided when to conduct QC inspections and you know what you’re looking for, you’re ready to implement quality control inspections in your warehouse.Just like you’ve dedicated space for operational processes like receiving and packaging orders, you’ll need to allocate space on the warehouse floor where quality personnel can safely inspect inventory without obstructing other machines, personnel, or processes in the warehouse.For each inspection point, you’ll want to create a quality control checklist that translates your quality standards into clear and objective criteria for the inspection. On your checklist, along with verifying that quality standards have been met, you’ll want to leave extra space for quality personnel to describe the details of any quality issue or deviation from SOPs discovered during the inspection.
Documenting Quality Results
As you execute and complete quality control inspections in the warehouse, the results of those inspections must be accurately and completely documented for ongoing review by quality experts and warehouse management personnel.You’ll certainly want to store copies of your warehouse quality inspection checklists for further review, but it can also be helpful to use a check sheet or tally sheet to keep track of which quality issues are discovered most frequently during inspections.The easiest way to keep track of your quality documentation is to document quality control inspections electronically using warehouse management software. Deploying mobile workstations in your warehouse allows your quality control teams to bring digital technology directly to the point of inspection, create and store inspection checklists in digital format, and maximize the accuracy and efficiency of quality control inspections.
Implementing Corrective/Preventive Actions
When a quality issue is discovered by your team, you’ll need a formalized system for implementing corrective and preventive actions that fix the problem and help prevent it from happening again.Simple quality issues like a mispicked or improperly packaged order can be corrected by having order picking or packaging staff repeat the process accurately or in accordance with established SOPs. Some process variance is normal and warehouse managers should expect the occasional inaccuracy or misjudgment from employees who are normally diligent about following processes.However, quality control inspections (especially when newly implemented) have the potential to uncover many or multiple different quality issues that often result from gaps in warehouse operational processes. When quality issues are abundant, quality personnel need to go beyond fixing individual issues and address underlying causes of quality issues to prevent future incidents. Quality personnel should conduct a root cause analysis to determine the underlying cause of quality issues, then implement preventive actions (e.g. additional employee training, staffing adjustments, process/SOP changes, etc.) to reduce future quality issues.
Measuring Quality Improvements
Measuring quality improvements in the warehouse is a critical aspect of demonstrating the overall impact of quality control on customer satisfaction, revenue, and profitability.If you’re looking at quality control in the warehouse receiving process, you’ll want to use metrics like receiving accuracy, productivity, and receiving cycle time to measure the impact of quality control. You may also want to track a downstream metric like putaway accuracy to assess whether quality control in the receiving process is boosting the accuracy or efficiency of downstream processes.If you’re looking at quality control for outgoing shipments, tracking warehouse efficiency metrics like order picking accuracy, pick rate, return rate, and perfect order rate can help you evaluate and demonstrate how your quality control efforts are driving genuine quality improvements and helping your bottom line.
Creating a Quality Culture
Managers seeking to implement warehouse quality control often overlook the importance of implementing a quality culture. A quality culture is a workplace culture where team members understand the importance of quality and strive to achieve high levels of quality in everything they do.In a strong quality culture, warehouse employees understand how their individual actions contribute to overall quality and customer satisfaction. They take action and make decisions to benefit the end user, not just to satisfy management or fulfill process requirements. Most importantly, a quality culture is one where individuals take feedback and accept accountability for their actions with a shared goal of maximizing the organization’s overall performance and creating the best possible experience for customers.
5 Warehouse Quality Control Tools You Need
- Process Flowcharts and SOPs
- Process flowcharts and SOPs are the process documents that guide warehouse employees in the accurate and efficient execution of warehouse processes. Process flowcharts and SOPs may be expanded or updated as a preventive action to help prevent quality issues in the warehouse.
- Quality Control Checklists
- Quality personnel in the warehouse use quality control checklists in their inspections to track and indicate whether quality standards were satisfied in the inspection. Quality control checklists should be stored in a secure digital format, accessible for warehouse managers to reference or review.
- Check Sheets
- A check sheet, or tally sheet, is a document used to track how frequently specific quality issues arise over the course of several inspections. Keeping track of which quality issues appear most frequently helps quality teams focus their preventive actions and related initiatives in areas with the greatest impact.
- Pareto Charts
- A Pareto Chart is a bar graph showing how frequently certain types of quality issues arise in the warehouse. Pareto Charts are based on the 80/20 rule, which roughly states that “80% of outcomes result from 20% of causes”. In the context of warehouse quality control, the 80/20 rule suggests that fixing the most impactful 20% of underlying quality issues should reduce problematic findings in QC inspections by around 80%.
- Cause-and-Effect Diagrams
- Cause-and-Effect diagrams can be used by warehouse managers and quality personnel to conduct a root-cause analysis and determine the root cause of quality issues before implementing a corrective or preventive action.
Optimize Warehouse Quality with DTG Mobile Workstations
DTG’s Problem Solver warehouse cart is a battery-powered mobile workstation designed to support every process in warehouse operations, from receiving and putaway to picking, packing, and quality control. Our mobile carts are powered by MPower battery systems that deliver 100% uptime with safe and reliable LFP technology.
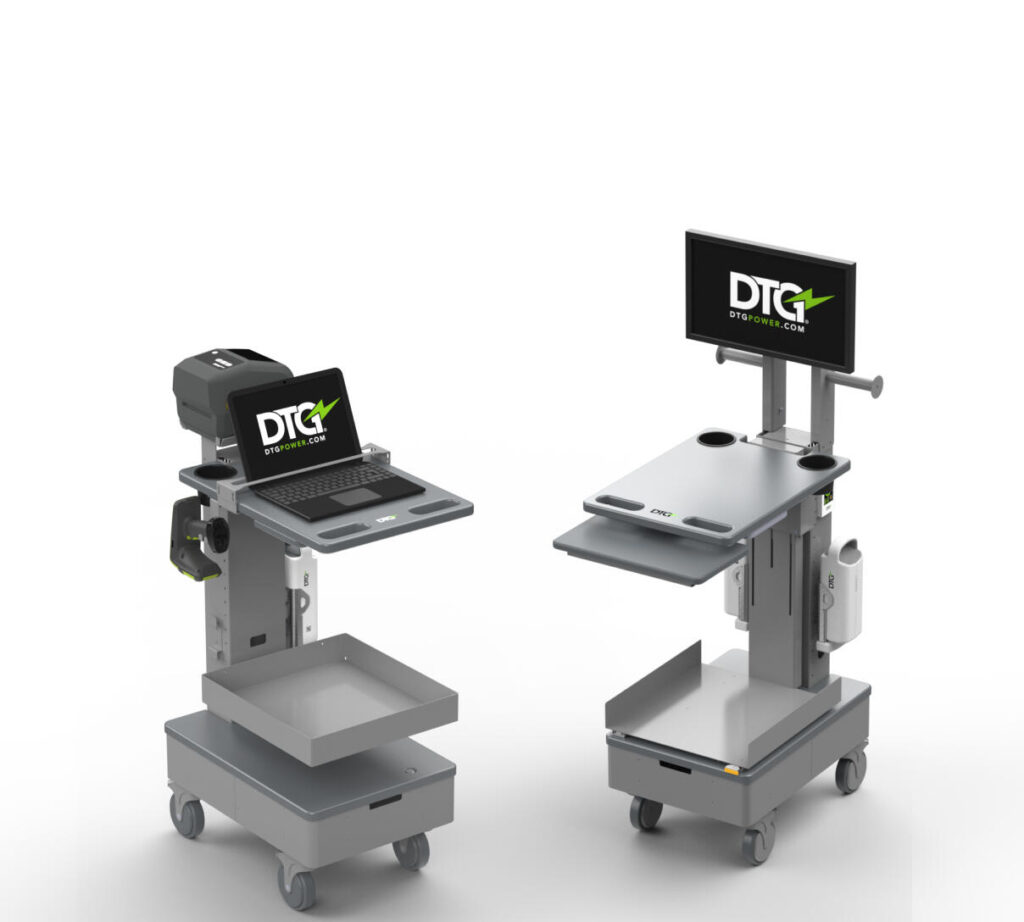
Our durable, ergonomic industrial workstations bring computer hardware, warehouse management software tools, and quality personnel together at the point of task, streamlining QC inspections and eliminating wasted steps to help QC teams operate more efficiently than ever before. Plus, our workstations are powered by our industry-leading MPower battery systems.With DTG’s mobile computer carts, warehouse quality teams can:
- Complete thorough quality inspections faster than ever before
- Accurately document and securely store the results of quality control inspection for review and analysis
- Document quality issues, root cause analysis, or recommend corrective/preventive actions from any location in the warehouse at any time
- Save time and eliminate wasted steps in the quality control process
[dt_divider style="thick" /]
Ready to learn more?
Contact us for a live demo of our DTG mobile workstations and we’ll show you exactly how our Problem Solver warehouse carts can help you achieve excellence in warehouse quality control.